In large plastic products factories, the mixing process of raw materials is an important part of the batching process. At present, the hybrid system of most factories adopts relay control, with many components, complicated lines and harsh on-site environment. The failure rate is high and maintenance and repair are difficult. In order to improve the on-site working environment and improve work efficiency, programmable controllers should be used to automate the entire mixing process. This design is the actual project of Tangshan Yulian Pipe Fitting Co., Ltd., PLC programming, modular structure, buzzer and indicator light combined alarm system. Both manual and automatic operation are available, and the two modes can be switched freely and interlocked. Passed the commissioning of the production site.
1 System working principle
The system is divided into two parts: high-speed mixing and cold mixing. The main equipments include high-speed mixers, cold mixers, testing equipment and dust collectors (self-contained systems).
1, 1 system automatic working process is as follows:
(1) Operation mode: the mixer and the cold mixer are automatically cut, and the mixer is cut and opened.
(2) Starting conditions:
a. Mixing machine and cold mixer maintenance cover close positioning. b. The mixer and the cold mixer are not overloaded abnormally.
c. The mixer temperature is not over temperature abnormal. d. The upper limit of the storage bin has not arrived.
(3) When the mixer start signal is ON, or when the mixer is turned ON, the mixer starts up at a low speed. After the low speed operation timing of the mixer arrives, the mixer runs at a high speed.
(4) When the mixer is mixed and the temperature set value is reached, or the mixing time is completed, the alarm sounds, and after 10 seconds, the alarm is automatically reset or the alarm reset button is reset to the alarm.
(5) When the alarm timing is completed, and the mixer discharge is cut open, the material is automatically discharged to the cold mixer. If the cold mixer is cut automatically, the cold mixer operation is triggered, if the mixer is not cut. When it is turned on, the alarm is activated, and the person is notified to cut it off, and the alarm can be reset.
(6) When the timing of the mixer discharge timer is completed, the mixer stops, and after the nozzle blows for 5 seconds, the discharge valve and the blow valve are closed, and the mouth blow is stopped.
(7) The cold mixer is running, the cooling temperature of the cold mixer arrives. After 10 seconds delay, the cold mixer automatically discharges the material, and the discharge timer is timed. When the timing of the cold mixer is reached, the cold mixer stops running. Close the cold mixer discharge valve and blow the cleaning discharge port.
1, 2 system equipment and main parameters
1.2.1 Mixer
Full capacity: 1050L Material input: 600-720L
Mixing weight: 360KG Mechanical weight: 5.6T
1) Drive unit
The Hegron hydraulic motor is used as the power unit. With its own power station, the hydraulic pump motor rated power is about 125/250HP, 4/8P. Double star wiring. Hydraulic oil temperature, oil level, pressure, flow, alarm, hydraulic motor start, ready and other signals are uploaded to the control room; control motor start, hydraulic motor start, hydraulic motor stop, emergency stop and other signals.
The mixer drive uses the NS-32420 motor buffer starter manufactured by ZEROSPAN.
2) Testing device
(1) The temperature detection signal uses the XMT-8000 series intelligent analog temperature controller.
a. Temperature control accuracy: resolution 512 Bit, actual control value ± 0.1%.
b. Control function: intelligent PID self-tuning, expert fuzzy control function.
c. Output mode: Analog output control: 4-20 mA current type, 0-5V voltage type.
d. Auxiliary function: sensor line open, short circuit automatic detection and buzzer alarm, super upper and lower limit buzzer alarm.
(2) The material level detection signal is measured by a PLS-3 type γ-ray material level meter for monitoring the mixer level.
1.2.2 Cold Mixer
Full capacity : 2000L Material input: 800-1400L
Mixing weight: 720KG Mechanical weight: 4T
1) The drive unit adopts a cage type three-phase asynchronous motor with rated power of 45HP and 4P.
2) The detection device temperature detection signal adopts XMT-8000 series intelligent analog temperature controller.
1.2.3 Dust collector
The dust collector adopts an automatic backwashing dust collector, which is installed on the mixing barrel and the cold mixing barrel to achieve fully enclosed dust-free mixing. The dust collector self-contained system is controlled by Mitsubishi FX2N-16MR PLC. This system provides power supply for it.
1.3 Interlocking requirements for mixer systems
(1) The conditions for the start of the mixer are: the maintenance cover of the mixer is closed and controlled by a solenoid valve.
(2) The conditions for the start of the cold-mixing machine are: the cold-mixer maintenance cover is closed and the upper limit of the storage tank is not reached. When the mixer discharges automatically, the cold-mixer is automatically triggered.
(3) When the system is running automatically, manual intervention is not allowed in principle to avoid system malfunction.
(4) When the mixer level gauge is turned on, the upper metering barrel discharge valve is automatically closed and the signal is fed back to the central control room.
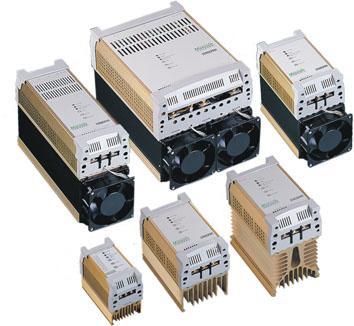